|
Ein Zerlegen des Kurbelgehäuses ist nötig wenn z.B. die
Hauptlagerschalen der Kurbelwelle zerschlissen sind oder Arbeiten an den
Kolben anfallen. Besonders nach einem Uebertritt von Kühlwasser ins
Motorenöl werden in der Regel die Lagerschalen so stark angegriffen, dass
ein Austausch unumgänglich ist.
Bevor man mit der Arbeit beginnen kann, muss zuerst der komplette Motor
ausgebaut werden. Danach müssen die Turbolader, Nockenwellen,
Zylinderköpfe, Oelpumpe, Oelwanne und Kupplung abgebaut werden.
Nachfolgend nun die nötigen Schritte um das Kurbelgehäuse zu überholen. |
|
Kurbelgehäuse demontieren: |
1. Drehen Sie die untere Befestigung des Oelmesstabs vollständig aus
(17er Schlüssel). |
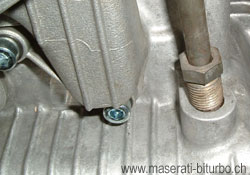 |
2. Lösen und entfernen Sie die Schraube der oberen Halterung des
Oelmesstabs (5er Inbus). |
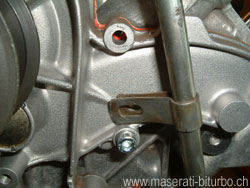 |
3. Ziehen Sie den Oelmesstab aus dem Kurbelgehäuse. Nehmen Sie danach
den Dichtungsring vom Oelmesstab ab oder ziehen Sie diesen, mit einem
Federhaken, aus dem Kurbelgehäuse. |
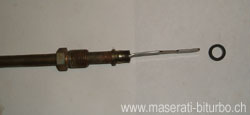 |
4. Falls das Kugellager der Getriebe-Dauereingriffswelle mangelhaft ist,
so sollte dieses mit einem entsprechenden Abzieher entfernt werden. |
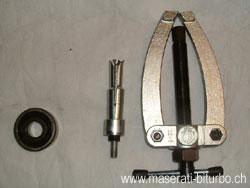 |
5. Die Abbildung rechts zeigt die Schwungradseite der Kurbelwelle ohne
Kugellager. |
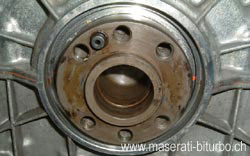 |
6. Lösen und entfernen Sie die Schrauben, deren Rippen- und
Unterlegscheiben der beiden seitlichen Motorträger (17er Schlüssel). |
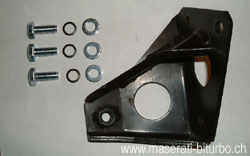 |
7. Entfernen Sie die Oelförderrohre zu den Turboladern (14er
Schlüssel). |
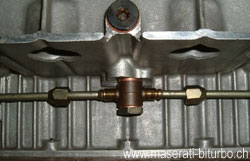 |
8. Lösen und entfernen Sie die Schraube des T-Stücks der
Oelförderleitungen (19er Schlüssel). Nehmen Sie danach das T-Stück ab. |
 |
9. Lösen und entfernen Sie die sechs äusseren Schrauben des
Kurbelgehäuses (6er Inbus). |
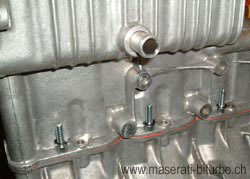 |
10. Lösen und entfernen Sie die acht mittleren Schrauben des
Kurbelgehäuses (6er Inbus). Die längeren der Schrauben befinden sich an
der Vorder- und Rückseite. Lösen und entfernen Sie danach die acht
inneren Muttern und deren Unterlegscheiben (19er Schlüssel). |
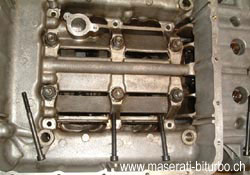 |
11. Ziehen Sie das Kurbelgehäuse vom Zylinderblock ab. Vorsichtige
Schläge mit einem Kunststoff- oder Bleihammer erleichtern diese Aufgabe.
Achten Sie dabei auf die hinteren Ausgleichslager. |
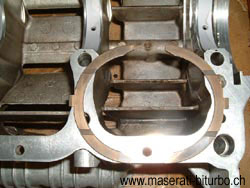 |
12. Entfernen Sie die vier Hauptlagerschalen aus dem Kurbelgehäuse.
Drehen Sie danach die Kurbelwelle, so dass der mittlere Pleuelzapfen nach
unten, in Richtung Zylinderblock, zeigt. Dies erleichtert später den
Ausbau der Kurbelwelle. |
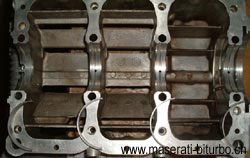 |
13. Wenn Leckagen bestehen, schlagen Sie die Büchsen des
Turboladerölrücklaufs, von der Innenseite her, aus dem Kurbelgehäuse. |
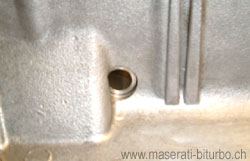 |
14. Lösen und entfernen Sie die zwölf
Pleueldeckel-Befestigungsschrauben (13er Schlüssel). |
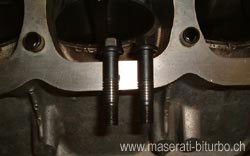 |
15. Nehmen Sie die Pleueldeckel von den Pleueln ab. |
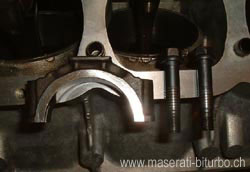 |
16. Entfernen Sie die Lagerschalen aus den Pleueldeckeln. Drücken Sie
danach leicht auf die Pleuel um die Kolben im O.T. zu positionieren. |
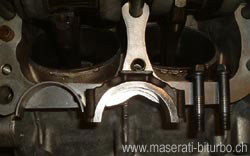 |
17. Heben Sie die Kurbelwelle vorsichtig aus dem Zylinderblock. Achten Sie auch
hier wiederum auf die beiden Ausgleichslager. |
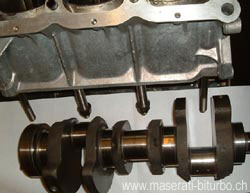 |
18. Nehmen Sie die zwei Ausgleichslager vom Zylinderblock ab. |
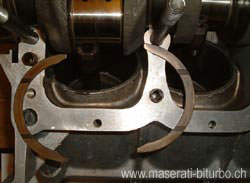 |
19. Entfernen Sie die vier Hauptlagerschalen aus dem Zylinderblock. |
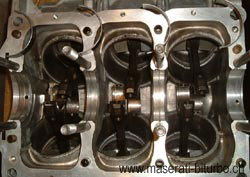 |
20. Nehmen Sie die Pleuellagerschalen von den Pleueln ab. |
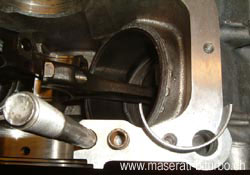 |
Es können nun weitere Arbeiten wie z.B. der Austausch der Kolben
durchgeführt werden. |
|
|
Kurbelgehäuse kontrollieren und reinigen: |
1. Reinigen Sie die Oeldurchgänge zwischen dem Kurbelgehäuse und der
Oelpumpe mit einer Bürste mit Spiralspitze und einer geeigneten
Flüssigkeit. Blasen Sie diese danach mit Druckluft durch, es sollten
keine Reste der Reinigungsflüssigkeit in den Durchführungen verbleiben. |
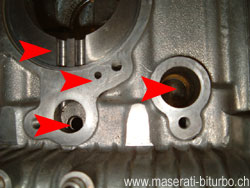 |
2. Reinigen Sie Oelförder- und Rücklaufkanäle wiederum mit einer
Bürste mit Spiralspitze und einer geeigneten Flüssigkeit. Blasen Sie
diese danach mit Druckluft sorgfältig durch, es dürfen keine Reste der
Flüssigkeit in den Kanälen verbleiben. |
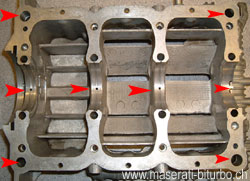 |
3. Entfernen Sie Reste der Flächendichtung an den Flanschen des
Kurbelgehäuses (im Bild rötlich eingefärbt) und des Zylinderblocks. Besprühen Sie dazu die Flansche
mit "Loctite Dichtungsentferner 7200" nach ca. 10 Minuten
Einwirkzeit können diese leicht mit einem Hartholz- oder
Kunststoffspachtel entfernt werden. Verwenden Sie keinesfalls eine Klinge
oder einen ähnlichen Gegenstand, die Fläche könnte sonst beschädigt
werden. Entfernen Sie ggf. auch Reste der Dichtung zwischen Kurbelgehäuse
und Oelwanne. Reinigen Sie danach das Kurbelgehäuse mit Motorenreiniger. |
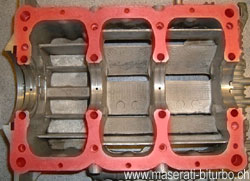 |
4. Reinigen Sie die Oeldurchgänge der Kurbelwelle mit einer
entsprechenden Flüssigkeit. Blasen Sie diese danach mit Druckluft durch,
es sollten keine Reste der Reinigungsflüssigkeit in der Kurbelwelle
verbleiben. |
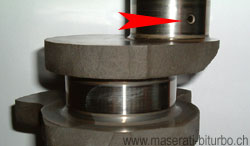 |
5. Messen Sie die Pleuelzapfen der Kurbelwelle mit einem Mikrometer aus. Wenn
Abweichungen oder Unrundheiten bestehen muss die Kurbelwelle ersetzt werden.
Das Mass der Pleuelzapfen muss zwischen 49.960 und 49.970 mm liegen (An der Arbeitsstelle der Pleuel
messen, nicht in der Mitte des Zapfens). |
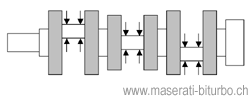 |
6. Messen Sie die Hauptlagerzapfen der Kurbelwelle mit einem Mikrometer
aus. Wenn Abweichungen oder Unrundheiten bestehen muss die Kurbelwelle
ersetzt werden. Das Mass der Hauplagerzapfen muss zwischen 69.970 und
69.980 mm liegen. |
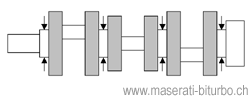 |
7. Das Kurbelgehäuse auf den Zylinderblock setzen und die inneren acht
Unterlegscheiben und deren Muttern eindrehen. Die Muttern mit einem
Anzugsmoment von 10 kg/m anziehen. Mit einer Innenmessuhr die vier
Aufnahmen der Hauptlagerschalen messen. Der Duchmesser (A) sollte 73.720 bis
73.730 mm betragen. Danach die Muttern wieder entfernen und das
Kurbelgehäuse vom Zylinderblock abnehmen. |
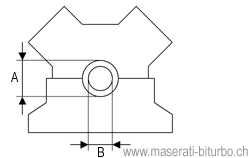 |
|
Kurbelgehäuse montieren: |
1. Drücken Sie leicht auf die Pleuel um die Kolben im O.T. zu
positionieren. Schmieren Sie die Pleuellagerschalen gut mit Motorenöl und
drücken Sie diese danach in die Pleuel. Achten Sie dabei auf die richtige
Ausrichtung der Aussparung. |
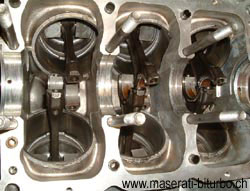 |
2. Schmieren Sie die vier Hauptlagerschalen gut mit Motorenöl und
drücken diese danach in den Zylinderblock. Achten Sie auch hier wieder
auf die richtige Positionierung der Aussparung. |
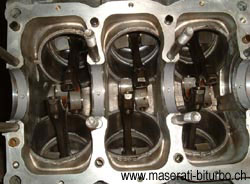 |
3. Befestigen Sie die Pleuel des Zylinders 1 und 3, mit einem Stück
Draht am Zylinderblock. |
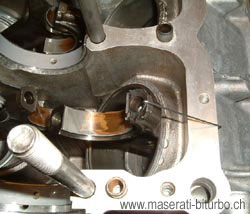 |
4. Halten Sie die Kurbelwelle mit dem mittleren Pleuelzapfen nach unten,
zum Zylinderblock zeigend. Legen Sie nun die Kurbelwelle vorsichtig in den Zylinderblock. |
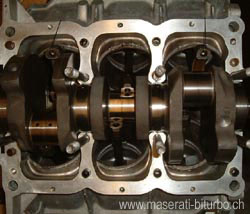 |
5. Entfernen Sie die, unter Punkt 3, montierten Drähte am Pleuel 1 und
3. Drücken Sie danach leicht auf die Kolben um die Pleuel mit den
Lagerzapfen zu verbinden. |
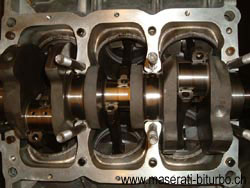 |
6. Schmieren Sie die beiden hinteren Ausgleichslager gut mit Motorenöl.
Drehen Sie diese danach in den Zylinderblock ein. Achten Sie darauf dass
die Seite mit den zwei Einbuchtungen jeweils zur Kurbelwelle zeigt. |
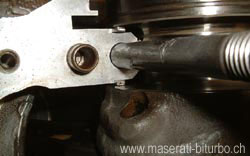 |
7. Schmieren Sie die Pleuellagerschalen gut mit Motorenöl und drücken
diese danach in die Pleueldeckel. |
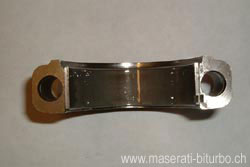 |
8. Setzen Sie die Pleueldeckel wieder auf die entsprechenden Pleuel auf.
Die Nummern von Pleuel und Deckel müssen übereinstimmen. |
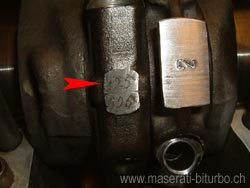 |
9. Kontrollieren Sie sicherheitshalber nochmals ob alle Nummerierungen
der Pleuel mit jenen der Deckel übereinstimmen. |
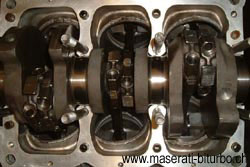 |
10. Schmieren Sie die Schrauben der Pleuel gut mit Motorenöl und drehen
diese danach ein. Ziehen Sie nun die Schrauben (13er Schlüssel), mit einem Anzugsmoment von
6.5 kg/m an. |
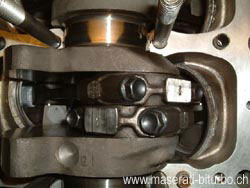 |
11. Messen Sie das axiale Spiel der Pleuelpaare, es muss 0.13 bis 0.25
mm betragen. Messen Sie danach das axiale Spiel der Kurbelwelle, dieses
muss 0.12 bis 0.18 mm betragen. Bei Abweichungen müssen die hinteren vier
Ausgleichslager ersetzt werden (Punkt 6 und 15). |
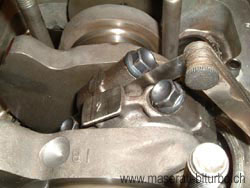 |
12. Falls entfernt, Schlagen Sie nun die neuen Büchsen des
Turboladerölrücklaufs in das Kurbelgehäuse. |
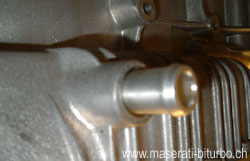 |
13. Reinigen Sie die Flansche des Zylinderblocks und Kurbelgehäuses mit
einem entfettenden Mittel wie z.B. Trichloräthylen. Legen Sie eine Tube
"Loctite 510" bereit. |
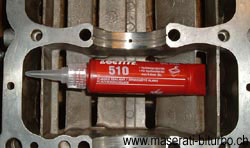 |
14. Tragen Sie, mit einem Pinsel oder einer Rolle, eine gleichmässige
Schicht "Loctite 510" auf den Flansch des Kurbelgehäuses auf. |
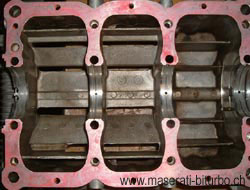 |
15. Schmieren Sie die vier Hauptlagerschalen gut mit Motorenöl und
drücken diese danach in das Kurbelgehäuse. Achten Sie wiederum auf die
richtige Ausrichtung der Aussparung. |
 |
16. Bestreichen Sie die beiden hinteren Ausgleichsscheiben gut mit Fett
und drücken diese danach in die Aussparung am Kurbelgehäuse. Achten Sie
darauf dass die Seite mit den Einbuchtungen jeweils zur Kurbelwelle zeigt. |
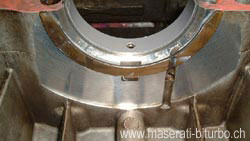 |
17. Setzen Sie das Kurbelgehäuse vorsichtig auf den Zylinderblock, die
beiden, unter Punkt 15 montierten Ausgleichsscheiben dürfen nicht
herunterfallen. |
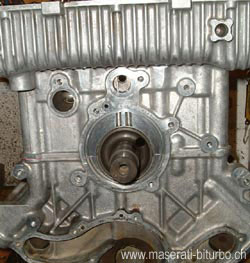 |
18. Legen Sie die Unterlegscheiben auf die Gewindestangen und drehen
danach die Muttern ein. Die beiden hinteren Muttern und Unterlegscheiben
(7 und 8) sollten durch neue ersetzt oder mit "Loctite
Gewindedichtung 572" abgedichtet werden. Ziehen Sie danach die
Muttern (19er Schlüssel) mit einem Anzugsmoment von 10 kg/m, in der Reihenfolge
1-2-3-4-5-6-7-8 an. |
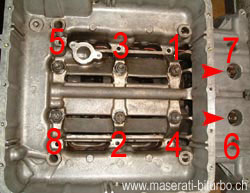 |
19. Drehen Sie die acht mittleren Schrauben mit deren Federscheiben ein.
Die vier längeren Schrauben befinden vorne und hinten (5, 6, 7 und 8).
Ziehen Sie nun die Schrauben (6er Inbus), in der Reihenfolge 1-2-3-4-5-6-7-8, mit
einem Anzugsmoment von 2.6 - 2.8 kg/m an. |
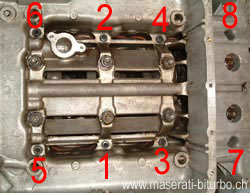 |
20. Drehen Sie die sechs äusseren Schrauben mit deren Federscheiben
ein. Ziehen Sie diese danach mit einem Anzugsmoment von 2.6 - 2.8 kg/m an
(6er Inbus). |
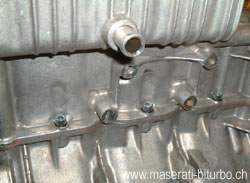 |
21. Falls Sie das Kugellager der Getriebe-Dauereingriffswelle entfernt
haben, so montieren Sie nun ein neues Lager mit Hilfe des entsprechenden
Werkzeugs. |
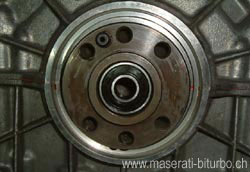 |
22. Bestreichen Sie einen neuen Simmerring mit Oel und führen diesen
danach vorsichtig auf die Kurbelwelle, die Dichtlippe darf keinesfalls
beschädigt werden. Setzen Sie nun das entsprechende Montagewerkzeug auf
die Kurbelwelle auf und drehen danach die Schrauben in der Reihenfolge 1-2-3-4 um je eine
halbe Umdrehung ein. Wiederholen Sie diesen Vorgang bis der Simmerring
komplett eingeführt ist. |
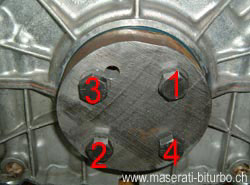 |
23. Nehmen Sie das Montagewerkzeug wieder ab. |
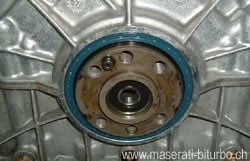 |
24. Bringen Sie das T-Stück der Förderleitungen, unter Verwendung von
zwei neuen Kupferdichtringen, wieder an (19er Schlüssel). Achten Sie bei der Montage darauf
dass das T-Stück parallel zur Oelwanne verläuft. |
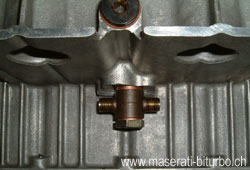 |
25. Setzen Sie die Oelförderrohre wieder in das T-Stück ein, ziehen
Sie danach die Muttern mässig an (14er Schlüssel). |
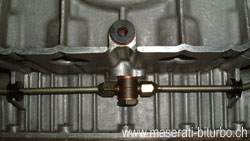 |
26. Befestigen Sie die beiden seitlichen Motorträger wieder am
Kurbelgehäuse, ziehen Sie die Schrauben (17er Schlüssel) mit einem
Anzugsmoment von 5 kg/m an. Empfehlenswert ist hier die Verwendung neuer
Rippen- und Unterlegscheiben. |
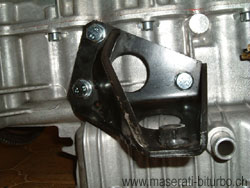 |
27. Setzen Sie einen neuen Dichtungsring auf den Oelmesstab auf. |
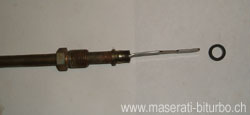 |
28. Drücken Sie den Oelmesstab ins Kurbelgehäuse, ziehen Sie danach
die Schraube mässig an (17er Schlüssel). |
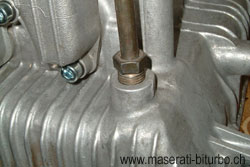 |
29. Befestigen Sie die obere Halterung des Oelmesstabs wieder, mit der
entsprechenden Schraube und deren Federscheibe an der, Wasserpumpe. Ziehen
Sie die Schraube (5er Inbus) mässig an. |
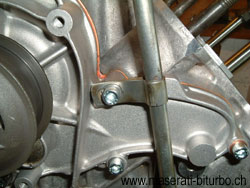 |